Metal 3D printing powder supplier
Metal3DAdditive manufacturing (AM) printing technology is reshaping the future of industrial manufacturing. As a leading enterprise with years of experience in metal material R&D12a leading enterprise,*Changsha Tianjiu Metal Materials Co., Ltd.*focuses on providing*metal3D3D printing technology solutions*and customized high-purity metal powder materials. Whether it's the integrated forming of complex structural components or the precise matching of special alloy materials, we empower your innovation with our technical strength.

---
2. Metal3D3D Printing Technology Explained
2.1Technical Principles and Core Advantages
metal3DPrinting is done through*Selective Laser Melting (SLM)*or*Electron Beam Melting (EBM)*) technology, layer by layer accumulating metal powder to achieve moldless forming of complex geometric structures. Compared with traditional processing methods, its core advantages include:
-Revolutionary Design Freedom: Breaking through the limitations of traditional cutting and casting processes, it can manufacture highly complex components such as internal honeycomb structures and conformal cooling channels.
-High Material Efficiency: Material utilization rate reaches95%above, significantly reducing the loss cost of high-end alloys.
-Lightweight and Performance Optimization: Integrated molding reduces assembly interfaces and improves component strength, suitable for fields such as aerospace and medical devices that are sensitive to weight.
-Rapid Iteration Capability: The cycle from design to finished product is shortened by50%-70%accelerating product R&D and prototyping.
2.2Mainstream Processes and Applicable Scenarios
- SLM(Selective Laser Melting): Uses a high-power laser beam to melt metal powder, with accuracy up to ±0.05mm,suitable for small and medium-sized precision parts such as titanium alloys and stainless steel (such as dental implants and sensor housings).
- EBM(Electron Beam Melting): Uses an electron beam as a heat source in a vacuum environment, with high forming efficiency and low residual stress, suitable for large-size high-temperature alloy components (such as aero-engine blades).
- DED(Directed Energy Deposition): Used for large component repair or hybrid manufacturing, allowing for real-time material addition and compatible with titanium and nickel-based alloys.
2.3Typical Applications
-Aerospace: Lightweight cabin brackets, fuel nozzles, turbine blades, materials includeTC4Titanium alloy,Inconel 718high-temperature alloys.
-Medical and Health: Biocompatible titanium alloy bone implants, personalized surgical guides, meetASTM F136medical certification standards.
-Automotive Industry: Lightweight aluminum alloy structural parts, high-temperature resistant mold inserts, shortening the cooling cycle30%above.
-Energy Equipment: Nuclear power valve components, hydrogen fuel cell bipolar plates, using316Lstainless steel anti-corrosion solutions.
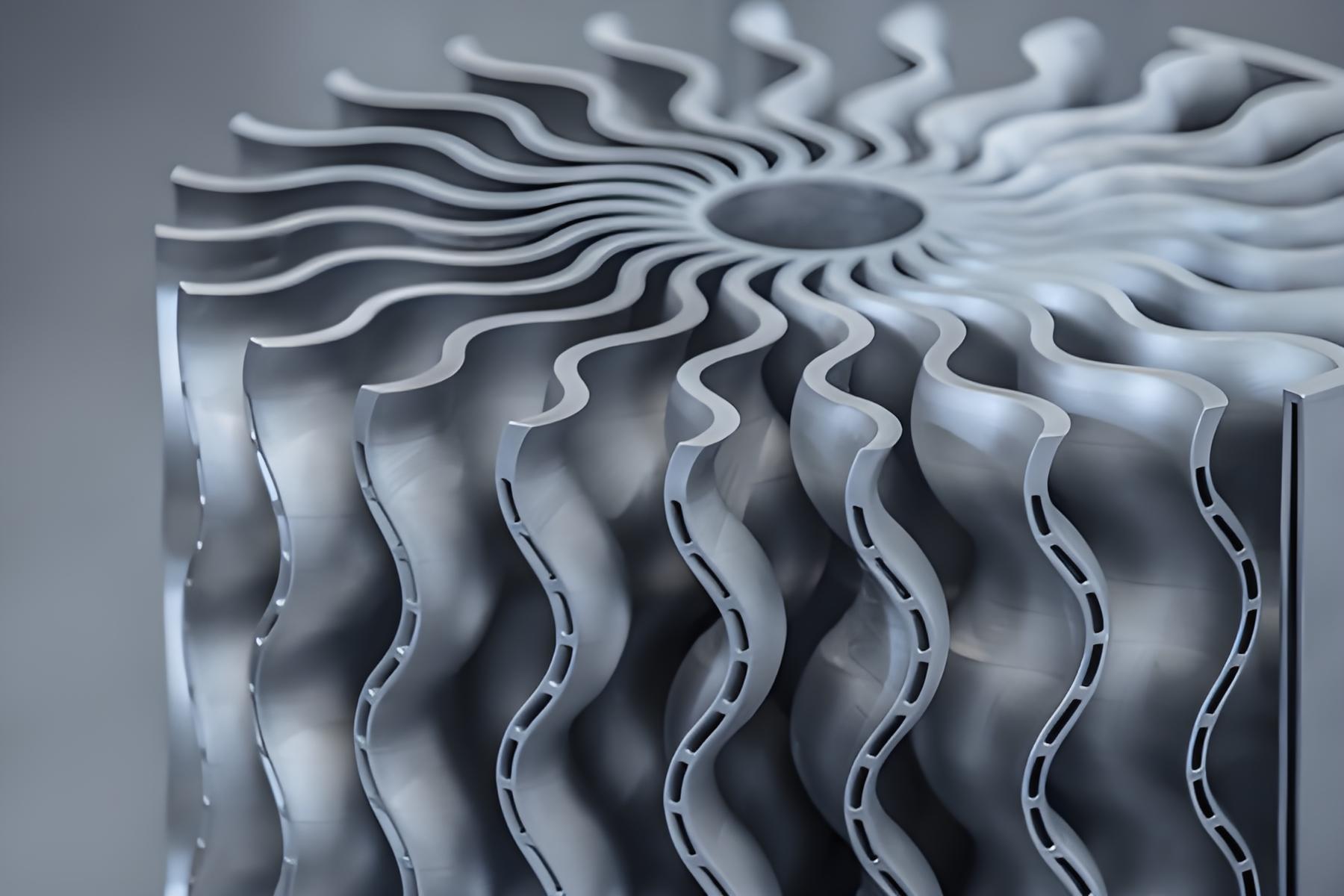
---
3.metal3DPrinting Powder Material Full Analysis
3.1Key Performance Indicators of Powder
-Sphericity >98%: Ensures powder fluidity, reducing interlayer defects in printing.
-Particle Size Distribution15-53μm: Compatible with mainstreamSLMequipment (such asEOS M290、Renishaw AM400).
-Oxygen content <1000ppm: Strictly control impurities to avoid increased brittleness of printed parts.
-Batch Consistency: Through laser particle size analyzer, scanning electron microscope (SEM) full inspection to ensure stable performance.
3.2Changsha Tianjiu Core Material System
-Titanium Alloy Series
- TC4(Ti6Al4V):A balance of strength and biocompatibility, suitable for orthopedic implants and satellite brackets.
- TA15(Ti6Al2Zr1Mo1V):High temperature resistance up to500°C,used for compressor blades of aero-engines.
-Stainless Steel Series
- 316LExcellent corrosion resistance, meeting the needs of marine engineering and chemical reactors.
- 17-4PHCan be strengthened through aging toHRC 40,used for high-strength die inserts.
-High-temperature Alloy Series
- Inconel 718:650°CMaintains high strength at low temperatures, the preferred material for gas turbine blades.
- Hastelloy XOutstanding oxidation and thermal fatigue resistance, suitable for combustion chamber components.
-Customized services: Support for customer-specified alloy development (such asCuCrZrheat-conducting alloys, high-entropy alloys), providing full-process support from powder preparation to printing parameter optimization.
3.3Material Selection and Technical Support
-Free Samples: After submitting your needs,48hours, we will send you suitable powder samples.
-Technical Service Support: Our own technical team,24hours online Q&A.
---
4.Core Advantages of Changsha Tianjiu
-R&D Strength:15Years of experience in metal powder preparation, our own factory production and sales, throughISO 9001、AS9100DAerospace Quality Management System Certification.
-Production Guarantee: Independently built inert gas atomization (VIGA) production line, with an annual output of high-purity powder exceeding500tons, with particle size control accuracy of ±2μm。
-Fast Response: Small batch orders3days delivery, supporting1kgminimum order, reducing customer trial and error costs.
-Full Process Service: From powder production and sales → quality control and management → one-to-one after-sales service → inspection report
---
5.Technical Q&A (FAQ)
Q1:Metal3DCan the mechanical properties of 3D printed parts reach the level of forgings?
ABy optimizing process parameters and post-processing,TC4The tensile strength of titanium alloy printed parts can reach1100MPaabove, elongation >8%,performance comparable to traditional forgings.
Q2How to control the performance degradation when recycling powder?
AWe recommend mixing new and old powders in a ratio of1:3and provide oxygen content detection services to ensure that the oxygen increment of recycled powder <150ppm。
*The above pictures are from Baidu. If there is any infringement, please contact us for deletion.
Recommend products
1. Excellent Corrosion Resistance: High molybdenum (Mo) content enhances resistance to pitting and crevice corrosion, suitable for harsh environments such as marine and chemical applications. 2. Biocompatibility: Certified for biocompatibility according to ISO 10993, suitable for manufacturing medical devices and implants. 3. High Purity and Low Impurities: Oxygen content ≤0.1%, carbon content ≤0.03%, reducing printing defects and ensuring the density and strength of finished products. 4. Excellent Processing Performance: High sphericity (≥95%), good fluidity (Hall flow rate ≤25 s/50g), suitable for additive manufacturing processes such as SLM and EBM.
View Details1. Ultra-high strength: Tensile strength ≥1900 MPa and hardness ≥50 HRC after aging treatment, suitable for high-load scenarios. 2. Excellent machinability: High sphericity (≥95%) and low oxygen content (≤0.1%), suitable for 3D printing and complex structure forming. 3. High-temperature performance: Good high-temperature stability, suitable for mold hot-working parts and parts used in high-temperature environments. 4. Heat treatment friendly: Can be rapidly strengthened by aging treatment (480-500℃) to improve mechanical properties.
View Details1. High-Temperature and Corrosion Resistance Temperature range: -200°C to 1000°C, oxidation and sulfidation corrosion resistance. Resistant to seawater, chlorides, and acidic media corrosion, suitable for marine and chemical environments. 2. Excellent Processability High sphericity (≥98%), low oxygen content (≤0.1%), good fluidity, reducing 3D printing defects. Strong bonding strength with the substrate, supporting the formation of high-precision complex structures. 3. High Strength and Toughness Room temperature tensile strength ≥900 MPa, maintaining excellent mechanical properties at high temperatures.
View Details1. High-Temperature Performance Applicable temperature range: -250°C to 700°C, resistant to high-temperature oxidation, creep, and sulfide corrosion. Strength is significantly improved after age hardening (room temperature tensile strength ≥ 1300 MPa). 2. Corrosion Resistance Resistant to acids, alkalis, chlorides, and seawater corrosion, suitable for chemical, marine, and nuclear industries. 3. Process Compatibility High sphericity (≥97%), low oxygen content (≤0.1%), excellent fluidity, compatible with additive manufacturing processes such as SLM (Selective Laser Melting) and EBM (Electron Beam Melting). No tendency for cracking after welding, supports the precision forming of complex structures.
View Details