High-quality raw material supplier for the spraying industry
As a leading domestic supplier of metal powders, Tianjiu focuses on providing high-quality metal powder raw materials for the thermal spraying industry. Through advanced powder production processes and a strict quality control system, we ensure that each batch of powder has excellent fluidity, particle size distribution, and chemical composition, providing a reliable material basis for the spraying process.
Overview of Spraying Technology
Spraying technology is a surface engineering technology that uses a heat source to heat metal or non-metal materials to a molten or semi-molten state and then sprays them at high speed onto the surface of a substrate to form a coating. This technology is widely used in aerospace, automotive manufacturing, energy equipment, electronics and electrical appliances, and other fields, and can significantly improve the wear resistance, corrosion resistance, and high-temperature resistance of workpieces.
Classification and Characteristics of Mainstream Spraying Technologies
1.Plasma Spraying (APS)
Working principle: Uses a plasma arc to heat the powder to a molten state and high-speed spray it onto the substrate surface to form a coating.
Temperature range: Plasma arc temperature can reach17000℃, suitable for high melting point materials.
Coating characteristics:
-Low porosity (1-3%)
-High bonding strength (30-50MPa)
-Suitable for preparing ceramic and cermet coatings
Typical applications:
-Aerospace: Thermal barrier coatings for turbine blades
-Medical field: Hydroxyapatite coatings for artificial joints
-Electronics industry: Insulating coatings for semiconductor devices
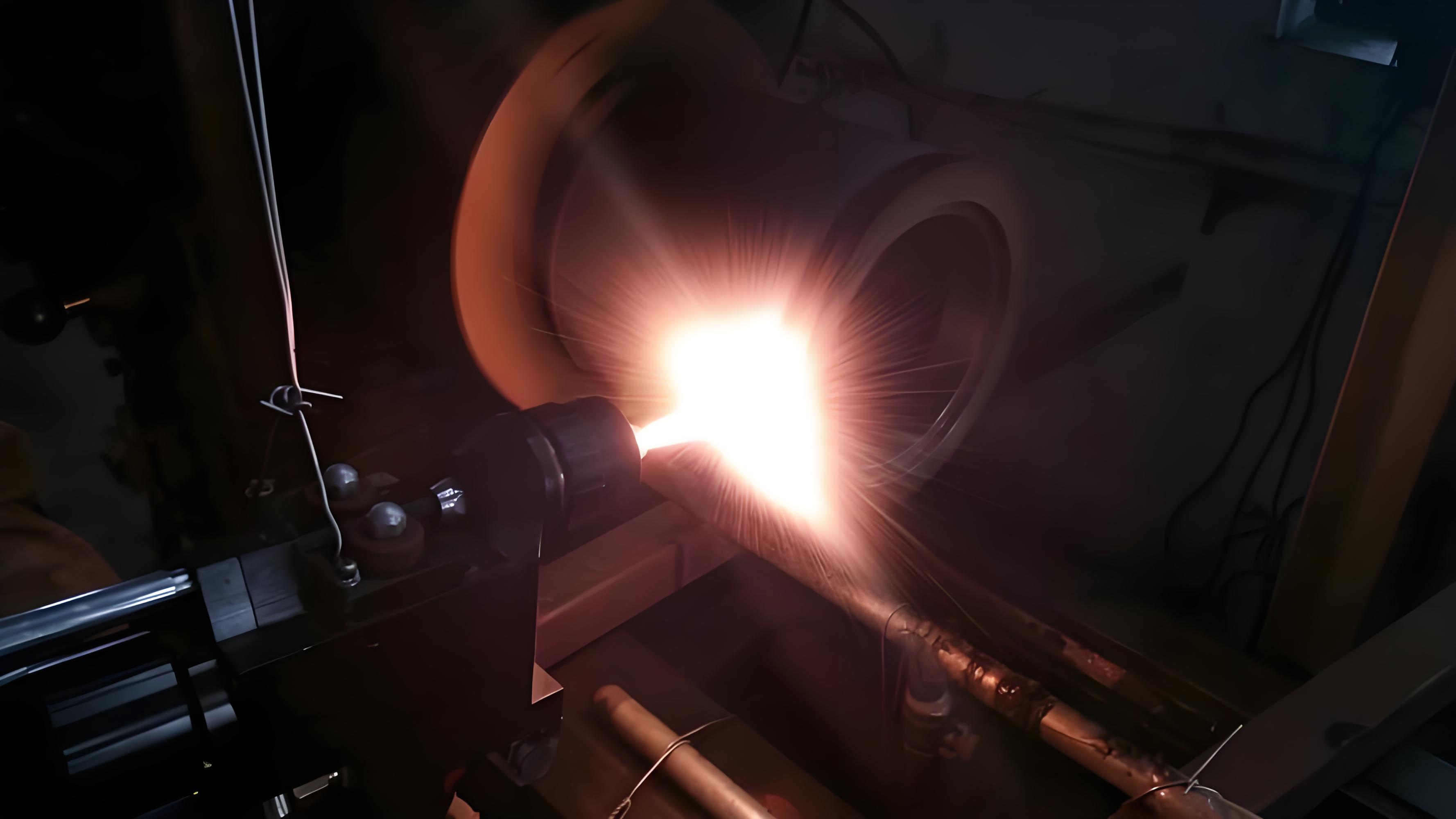
2.High-Velocity Oxy-Fuel Spraying (HVOF)
Working principle: Uses combustion gas to generate a supersonic flame, accelerating the powder to800-1200m/sand spraying it onto the substrate surface.
Temperature range: Flame temperature is approximately3000℃, suitable for cemented carbides such as tungsten carbide.
Coating characteristics:
-Extremely low porosity (<0.5%)
-High bonding strength (>70MPa)
-High hardness (Hv 1200-1400)
Typical applications:
-Petrochemical industry: Wear-resistant coatings for valves and pump bodies
-Automotive manufacturing: Engine piston rings, gear strengthening
-Energy field: Erosion-resistant coatings for water turbine blades
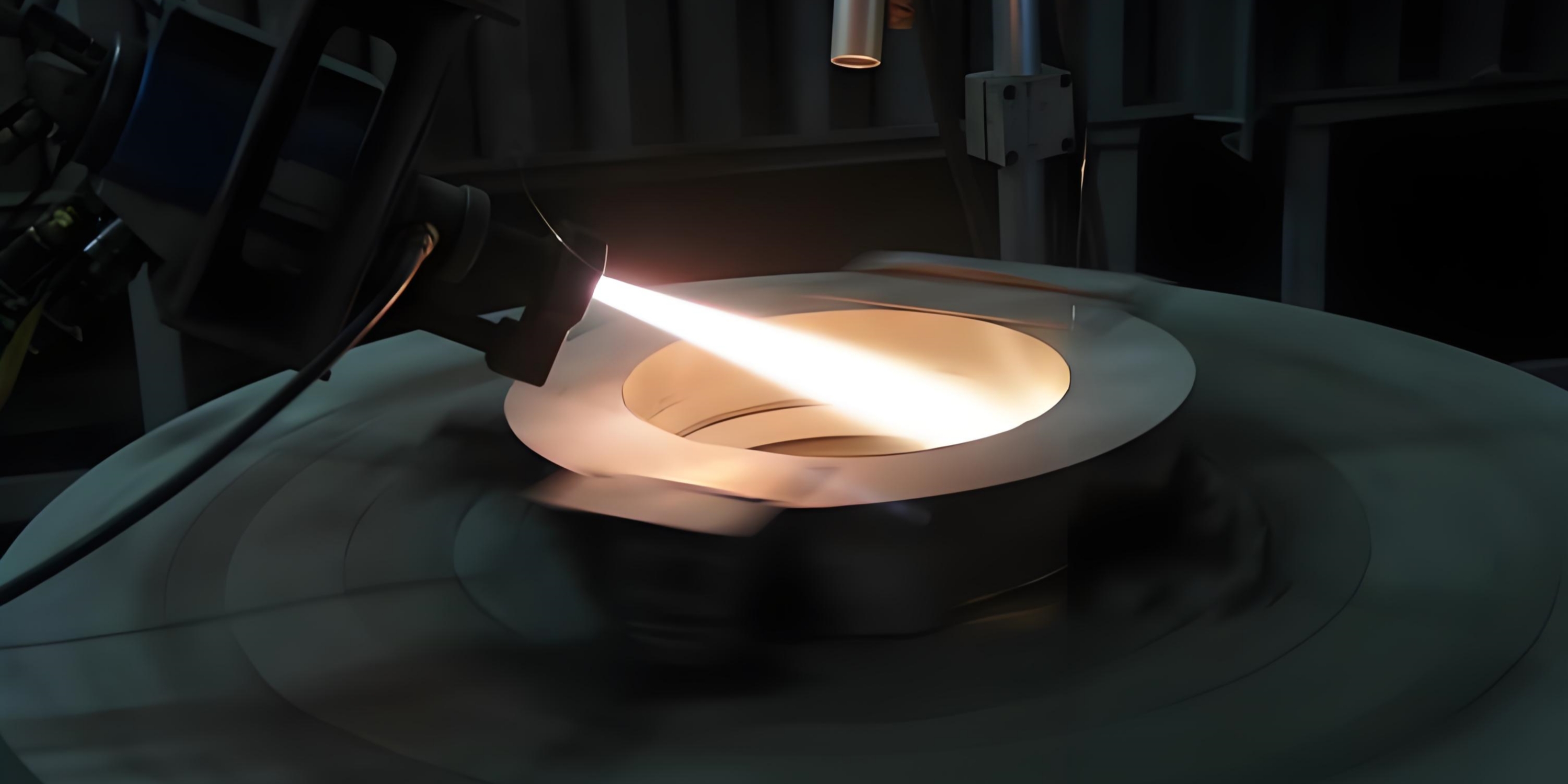
3.Arc Spraying
Working principle: Uses an electric arc to heat metal wire, using compressed air to atomize the molten metal and spray it onto the substrate surface.
Temperature range: Arc temperature is approximately6000℃, suitable for low melting point metals.
Coating characteristics:
-High deposition efficiency (>90%)
-Low cost, suitable for large-area construction
-Higher coating porosity (5-10%)
Typical applications:
-Corrosion protection of bridge steel structures
-High-temperature resistant coatings for boiler pipes
-Anti-slip coatings for ship decks
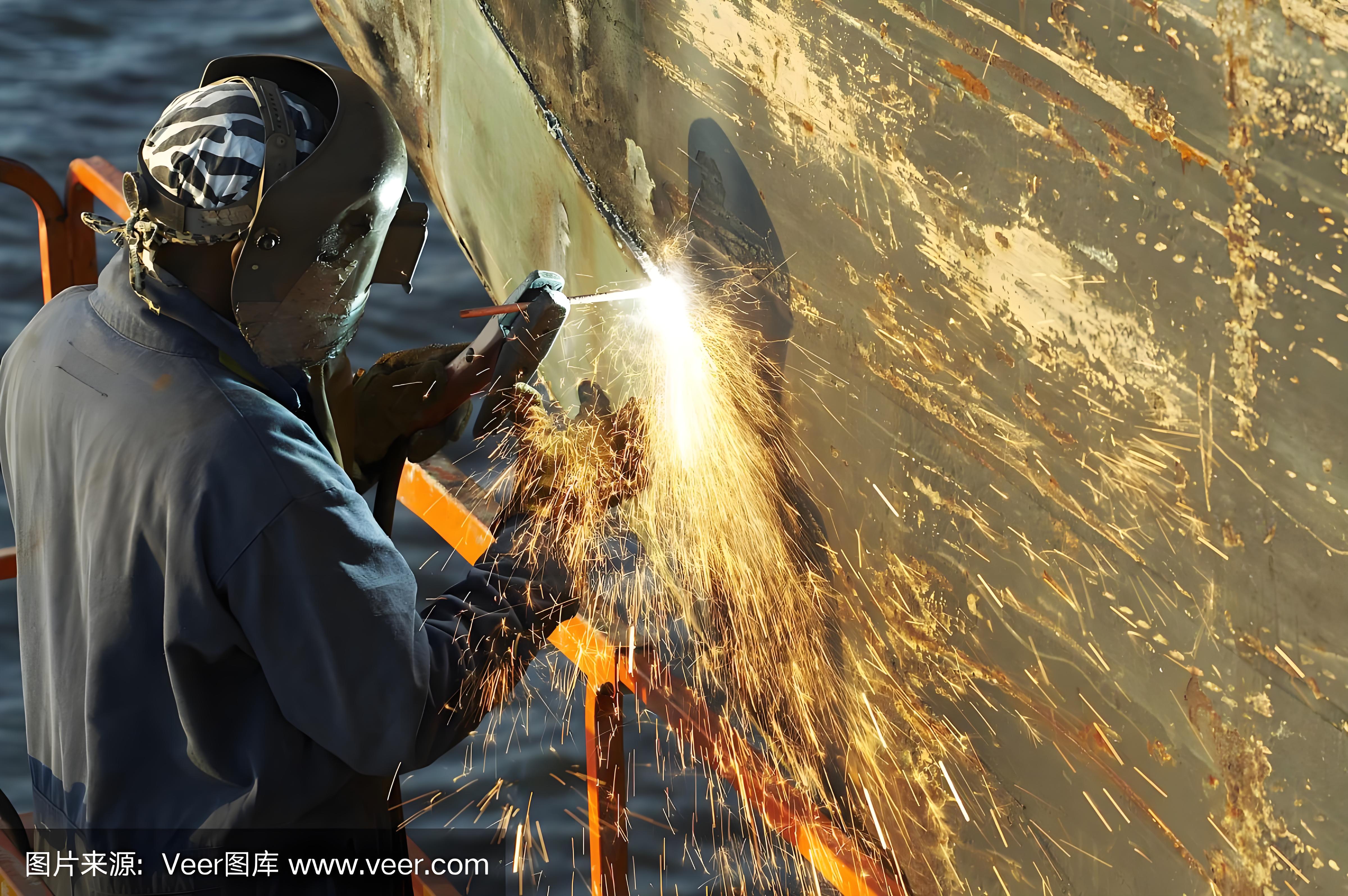
4.Cold Spraying Technology
Working principle: Uses high-pressure gas to accelerate the powder to supersonic speed, forming a coating through kinetic energy rather than thermal energy.
Temperature range: Working gas temperature <600℃, no thermal deformation of the substrate.
Coating characteristics:
-No oxidation, suitable for active metals (such as titanium and magnesium)
-Dense coating, porosity <1%
-High bonding strength (>50MPa)
Typical applications:
-Electronics and electrical appliances:5GBase station radiator coating
-Aerospace: Repair of titanium alloy components
-New energy: Conductive coatings for lithium battery current collectors
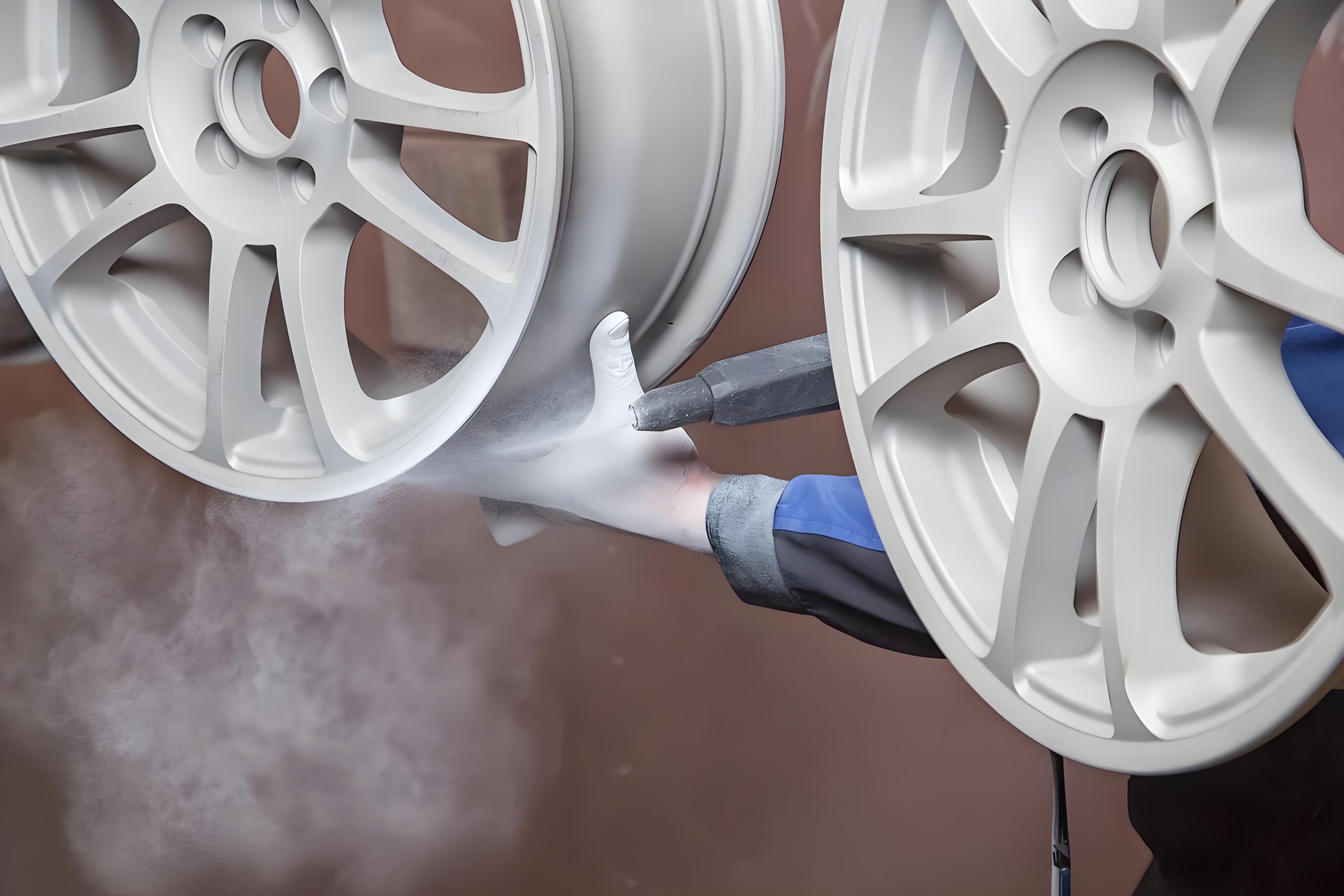
Core Advantages of Spraying Technology
1.Performance Improvement
-Wear resistance: Coating hardness can reachHRC 65and above
-Corrosion resistance: Salt spray test >2000hours
-High-temperature resistance: Maximum withstand temperature1400℃
2.Economic benefits
-Extend the service life of workpieces3-5times
-Reduce equipment maintenance costs40-60% `nbsp_tag
-Reduce downtime and improve production efficiency
3.Environmental Protection
-No harmful gas emissions
-Material utilization rate >90%
-Supports the repair of waste parts, reducing resource waste
Key material selection for spraying technology
1.Powder characteristics
-Particle size distribution:15-53μmIs the common range
-Sphericity: >90%Ensure fluidity
-Oxygen content: <800ppmGuarantee coating quality
2.Substrate matching
-The coefficient of thermal expansion is close, reducing stress cracking
-Surface pretreatment (sandblasting, cleaning) improves bonding strength
3.Process parameter optimization
-Spraying distance:100-150mm
-Powder feeding rate:30-50g/min
-Gas pressure:0.6-0.8MPa
Future trends in spraying technology
1.Intelligent: Robot automatic spraying, improving accuracy and consistency
2.Green: Development of low-energy consumption and low-emission processes
3.Composite: Application of new coating materials such as nanomaterials and amorphous alloys
*All the above pictures are from Baidu. Please Contact Us if there is any infringement.
Recommend products
1. Ultra-high purity: Silver content ≥99.95%, total impurities ≤500 ppm 2. Spherical morphology: sphericity >95%, good fluidity, suitable for screen printing, spraying and other processes 3. High conductivity/thermal conductivity: volume resistivity ≤1.6 μΩ·cm, thermal conductivity ≥420 W/(m·K) 4. Controllable particle size: standard particle size 0.1-20μm (customizable), low specific surface area, high sintering activity 5. Oxidation resistance: surface coated with anti-oxidation layer (optional), extending storage and processing stability
View Details