Professional MIM metal powder supplier
MIM Introduction to Metal Injection Molding
MIM ( Metal Injection Molding Metal Injection Molding (MIM) is an advanced manufacturing process that combines plastic injection molding technology with powder metallurgy. It is widely used to produce complex, high-precision, and high-performance metal components. Its core process consists of four steps:
1. Feedstock Preparation
Metal powders (such as stainless steel, iron-based alloys, copper-based alloys, etc.) are mixed with a polymer binder to form a uniform injection molding feedstock.
2. Injection Molding
The feedstock is injected into a mold using an injection molding machine to quickly form a green part with a precise structure.
3. De-binding
Thermal debinding or solvent debinding technology is used to remove the binder from the green part, leaving behind the metal skeleton.
4. Sintering
High-temperature sintering in a controlled atmosphere furnace densifies the metal particles, ultimately producing a finished product with near theoretical density.
Process Advantages:
✅ Can produce parts with complex geometries (difficult to achieve with traditional machining)
✅ Material utilization rate is high 95% resulting in significant cost savings
✅ Suitable for mass production with high consistency
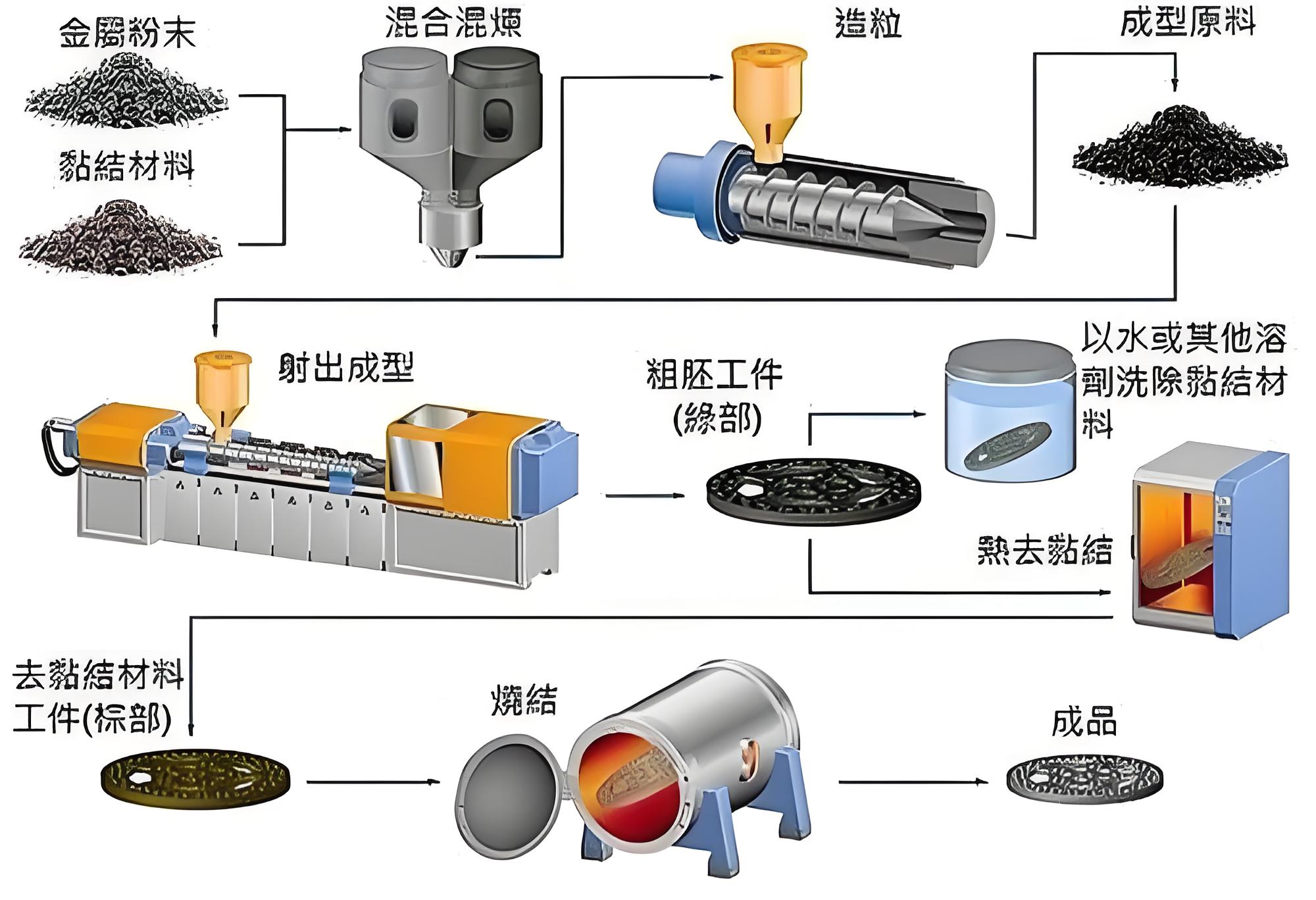
Tianjiu Metal MIM Dedicated Metal Powder Solutions
As a leading metal powder manufacturer in China, Changsha Tianjiu provides * high-performance, customized * metal powder materials to meet the needs of various industries: MIM Stainless Steel Series
1. Stainless Steel Powder
316L/304L :Excellent corrosion resistance, suitable for medical devices and watch parts. :High strength and wear resistance, used in aerospace and automotive precision parts.
17-4PH :Excellent corrosion resistance, suitable for medical devices and watch parts. Iron-based Alloy Series
2. Alloy Powder
Fe-Ni :Low coefficient of thermal expansion, suitable for electronic packaging and sensor components. :High temperature oxidation resistance, used in industrial cutting tools and machinery parts.
Fe-Cr :Low coefficient of thermal expansion, suitable for electronic packaging and sensor components. Special Alloy Series
3. Copper-based Powder
:High electrical and thermal conductivity, suitable for electronic connectors and heat dissipation components. Tungsten Alloy Powder
:Ultra-high density, used for counterweights and radiation shielding components. Typical Particle Size Range of Metal Powders
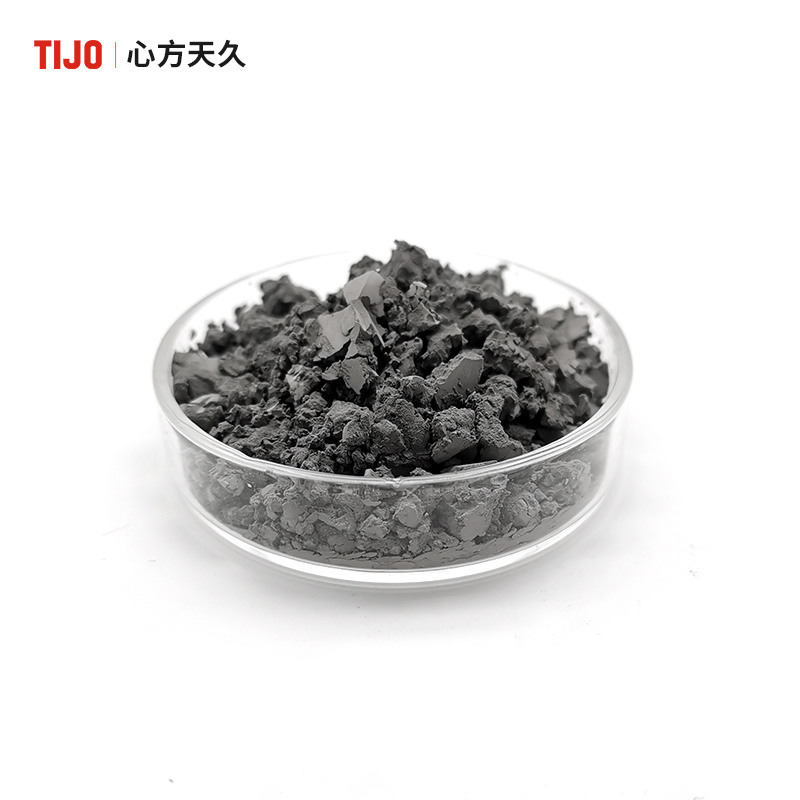
MIM The process has relatively strict requirements for powder particle size, which needs to balance flowability, packing density, and sintering activity:
MIM Average Particle Size (
1. ) D50 Typical Range:
5-25 microns (μ m ), with 10-20 μ being the most common. ), with Ultrafine Powder: Some high-precision applications (such as miniature electronic components) use
< D50 powder, but the cost is higher. 10 being the most common. ), with Particle Size Distribution:
2. The range needs to be strictly controlled
to avoid inconsistencies caused by excessively coarse or fine particles. D10-D90 Typical Distribution Example:
≥ D10 ≤ 3 being the most common. ), with ,D90 (Slightly different for different materials). 45 being the most common. ), with Powder Particle Size Advantages
Tianjiu Metal MIM Precise and Controllable:
1. Provides
'**D50 5-25' Customized particle size being the most common. ), with to support customers in selecting the optimal specifications according to product structure (such as thin-walled parts, complex cavities). ** Typical Material Examples:
Stainless Steel:
316L D50=15 D90=30 being the most common. ), with , m being the most common. D50=12
17-4PH D50=15 D90=25 being the most common. ), with , High sphericity: being the most common. D50=12
2. Spherical powder proportion >
(Detected by scanning electron microscopy), reducing injection defects and improving green compact strength. 90% Low oxygen content:
3. Oxygen content ≤
氧含量≤800ppm (Some materials can be ≤ 300ppm ), avoiding sintering embrittlement.
Industry Application and Particle Size Matching Suggestions
|
||
Application Areas
|
Recommended Particle Size
|
Tianjiu
|
Medical Devices ( Such as bone nails )
|
8-15 being the most common. ), with
|
316L、Ti-6Al-4V
|
Automotive gears / Turbine components
|
15-20 being the most common. ), with
|
17-4PH、Fe-Ni Alloy
|
Electronic precision parts ( SIM card tray )
|
5-12 being the most common. ), with
|
304L、Cu-Sn Alloy
|
High-density counterweight
|
20-25 being the most common. ), with
|
Tungsten alloy (W-Ni-Fe)
|
MIM Process Application Areas
- Medical industry: surgical instruments, dental implants
- Automotive manufacturing: turbocharger parts, fuel injectors
- Consumer electronics: mobile phone card trays, smart wearable structural parts
- Industrial equipment: gears, locks, precision hardware
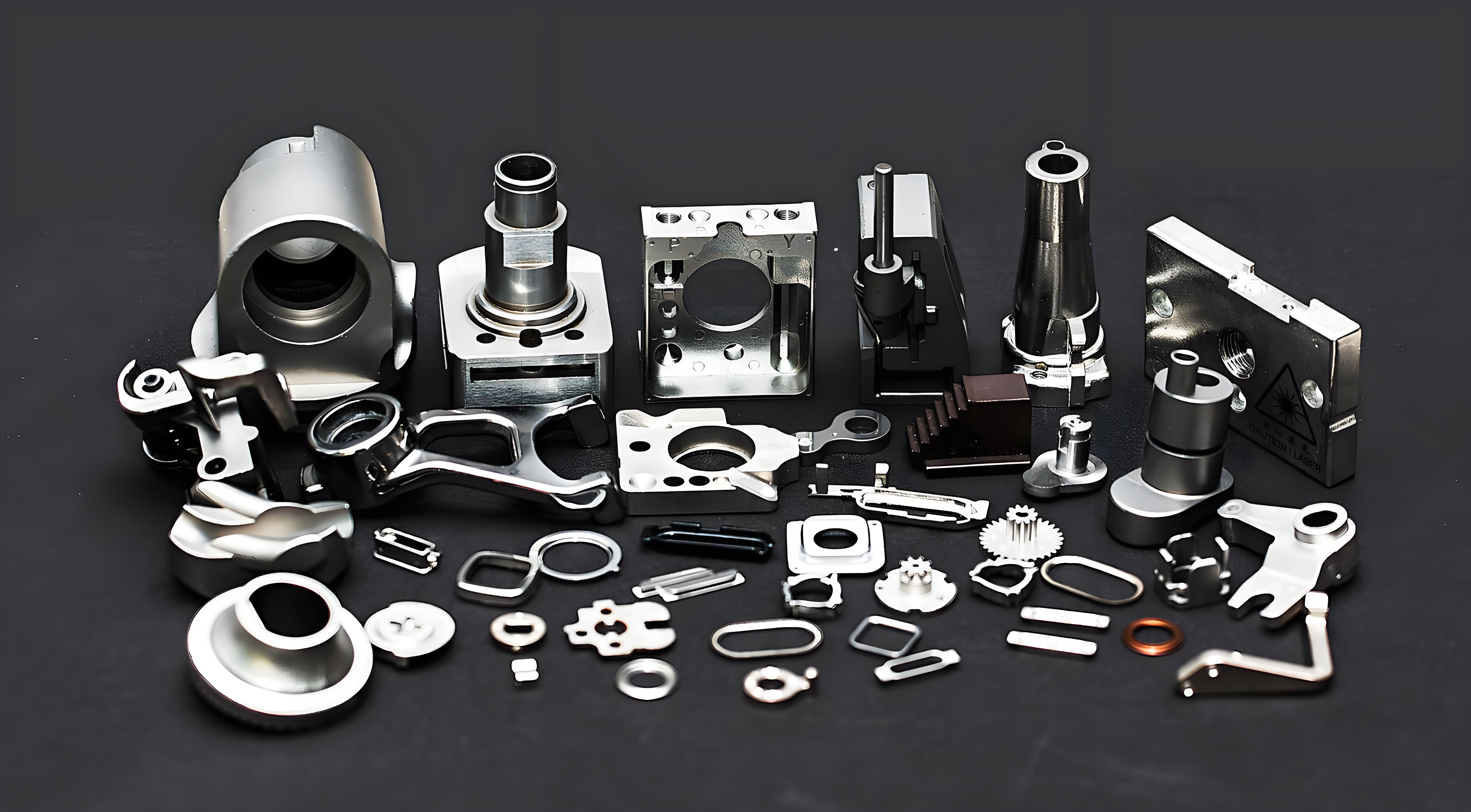
Why choose Tianjiu Metal's MIM powder?
Advanced powder technology: Using vacuum induction melting atomization ( VIGA ) technology to achieve high sphericity and narrow distribution powder production.
Strict quality control: Each batch of powder is tested by laser particle size analyzer ( Malvern Mastersizer ), Hall flow meter, etc.
Fast response: Provide particle size test reports to support customer process verification.
Tianjiu Powder Core Advantages:
Uniform particle size distribution ( D50 5-25 being the most common. ), with Customizable)
High sphericity, excellent fluidity, reduce injection defects
Strict quality control (compliant with ASTM/ISO standards)
Frequently Asked Questions ( FAQ )
Q : What is the delivery cycle of Tianjiu metal powder?
A : Conventional models 2-5 days, customized products about 3-4 weeks.
Q : Do you support small batch samples?
A : Provide 1kg minimum order quantity sample service, and provide process parameter suggestions.
Get your MIM solution immediately
Contact us: +86 18163731172
Email: sales01@hntijo.com
*The above pictures are from Baidu. If there is any infringement, please contact us for deletion.
Recommend products
1. Excellent Corrosion Resistance: High molybdenum (Mo) content enhances resistance to pitting and crevice corrosion, suitable for harsh environments such as marine and chemical applications. 2. Biocompatibility: Certified for biocompatibility according to ISO 10993, suitable for manufacturing medical devices and implants. 3. High Purity and Low Impurities: Oxygen content ≤0.1%, carbon content ≤0.03%, reducing printing defects and ensuring the density and strength of finished products. 4. Excellent Processing Performance: High sphericity (≥95%), good fluidity (Hall flow rate ≤25 s/50g), suitable for additive manufacturing processes such as SLM and EBM.
View Details1. Ultra-high strength: After aging hardening, the tensile strength ≥1310 MPa, hardness HRC ≥40, excellent impact toughness. Performance is stable at low temperatures down to 300°C, and fatigue resistance is outstanding. 2. Corrosion resistance: Resistant to atmospheric, seawater, and weak acid corrosion; suitable for chemical and marine environments. Passivation or plating further improves corrosion resistance. 3. Processing adaptability: High sphericity (≥95%), low oxygen content (≤0.1%), excellent fluidity, suitable for 3D printing of complex structures. Small heat treatment deformation, supports precision machining and surface polishing.
View Details1. Corrosion Resistance: Resistant to weak acids, alkalis, chlorides, and organic media corrosion. Its intergranular corrosion resistance is superior to 304 stainless steel. It exhibits good oxidation resistance and is suitable for humid and high-temperature steam environments. 2. Processing Adaptability: High sphericity (≥95%), low oxygen content (≤0.1%), and excellent fluidity reduce additive manufacturing defects. Excellent weldability, no annealing required after welding, and no tendency for hot cracking. 3. Environmental and Hygiene: Lead-free and cadmium-free, compliant with FDA and RoHS standards, suitable for food contact applications.
View Details